What Plastics Are Used For Thermoforming?
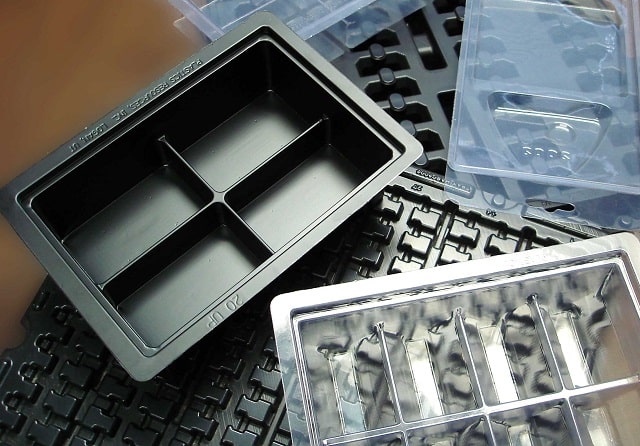
What Is Thermoforming?
Firstly, it is important you have an understanding of the thermoforming process which is in fact a very simple process. Thermoforming involves heating a material until it reaches its forming temperature, this then allows the hot sheet to push the material into cavities. This usually occurs in an aluminum form so the material changes to the shape of that particular mold. The material used also usually comes in rolls which are made in an extrusion facially or are purchased. Materials such as resin pallets and industrial regrind are very commonly used. The plastic sheet created is then placed in the thermoformer and heated in an oven where it will reach its optimum temperature and is then ready to be molded. Once plastic parts have been made out of the sheet trimming occurs where extra plastic is cut off and collected and recycled back into the thermoforming process so no plastic goes to waste. Applab provides more detailed information of the process of thermoforming if you are interested in furthering your thermoforming knowledge.
What Is PET Plastic?
PET plastic also known as polyethylene terephthalate is one of the most commonly used plastics for thermoforming. PET plastic is mostly used for packaging and bottle production as once molded this plastic has very strong resistance against substances such as water and oxygen. PET plastic is also the most commonly recycled plastic type among many others.
What Is PETG Plastic?
Another common type of plastic is PETG plastic also known as polyethylene terephthalate glycol has extremely good strength and resistance to stronger substances such as acids and alkalis. Polyethylene terephthalate glycol is relatively easy to thermoform and is a very stable and tough type of plastic when formed.
What Is Polypropylene?
Polypropylene is known as one of the highest volume plastics and is a translucent plastic and completely unpigmented. The translucency of this plastic is caused by the large capacity of crystallizes that interfere with the amount of light transmission causing the plastic to be translucent. The different classifications of polypropylene is homopolymer which is a type of polypropylene that is good for hot substances and used for microwave practices. On the other hand, impact copolymer is a type of polypropylene that is good for freezer appliances. Another classification of polypropylene is random copolymer which is also used for refrigerated appliances as it is a plastic that can keep cool. A less common classification of polypropylene is filled polypropylene which is when the plastic is filled with calcium carbonate making the plastic have much more stiffness and durability, making it a more suitable plastic for packaging goods.
What Is HIPS Plastic?
This plastic is known as a rather high impact type of polystyrene and is used for rigid plastic. This rigid form to this plastic makes it perfect as a protective plastic for food and drink packaging. This plastic is a good economical option and is a plastic that can be formed quite easier than other types of plastic.